Министерство образования и науки Российской Федерации
Федеральное государственное автономное образовательное учреждение
высшего профессионального образования
«Уральский Федеральный Университет
имени первого Президента России Б.Н. Ельцина»
Кафедра технологии вяжущих материалов и строительных изделий
РЕФЕРАТ
По дисциплине: Строительные материалы. Материаловедение.
Тема: «Керамические материалы. Свойства сырья: глины, отощающих, выгорающих и пластифицирующих добавок. Способы измерения и определения свойств»
Студент.
Группа
Преподаватель:
Екатеринбург, 2015 г
СодержаниеВведение........................................................................
.....................................3
Классификация керамических материалов и изделий...................................4-5
Виды керамических материалов и изделий ................................................6-11
Общие свойства керамических материалов и изделий..............................12-13
Сырье для изготовления керамики.............................................................14-16
Добавки, для улучшения свойств глины ....................................................17-22
Получение керамики. Порошки для изготовления керамики....................23-28
Общая технологическая схема изготовления керамических изделий........29-31
Заключение......................................................................
..................................32
Список
литературы………...................................................................
.............33
1.Введение
Керамическими называют материалы и изделия, изготовляемые формованием и обжигом глин. Глина– осадочная горная порода, состоящая из природных водных алюмосиликатов с различными примесями. Глина, замешанная с определённым количеством воды, образует глиняное тесто, обладающее связностью и пластичностью, способное в процессе обжига образовывать прочный искусственный камень.
Технология
производства керамических материалов связана с характеристиками используемых
глин (огнеупорность; содержание AlO и красящих оксидов в прокалённом состоянии,
водорастворимых солей, включений размером более 0,5 мм; размер включений;
пластичность; температура спекания; содержание свободного кремнезёма)
"Керамос"- на древнегреческом языке означало гончарную
глину, а также изделия из обожженной глины. В глубокой древности из глин путем
обжига получали посуду, а позднее (около 5000 лет назад) стали изготовлять
кирпич, а затем черепицу.
В строительстве широко применяются керамические материалы и изделия. Они обладают различными свойствами, которые определяются составом исходного сырья, способами его переработки, а также условиями обжига - газовой средой, температурой и длительностью. Материал (т.е. тело), из которого состоят керамические изделия, в технологии керамики именуют керамическим черепком.
Большая прочность, значительная долговечность, декоративность многих видов керамики, а также распространенность в природе сырьевых материалов обусловили широкое применение керамических материалов и изделий в строительстве. В долговечности керамических материалов можно убедиться на примере Московского Кремля, стены которого сложены почти 500 лет назад.
2. Классификация керамических материалов и изделий.
Среди сырьевых порошкообразных материалов - глина, которая имеет преимущественное применение при производстве строительной керамики. Она большей частью содержит примеси, влияющие на ее цвет и термические свойства. Наименьшее количество примесей содержит глина с высоким содержанием минерала каолинита и потому называемая каолином, имеющая практически белый цвет. Кроме каолинитовых глин разных цветов и оттенков применяют монтмориллонитовые, гидрослюдистые.
Кроме глины к применяемым порошкообразным материалам, являющимися главными компонентами керамических изделий, относятся кварциты, магнезиты, хромистые железняки.
Для технической керамики используют искусственно получаемые специальной очисткой порошки в виде чистых оксидов, например оксиды алюминия, магния, кальция, диоксиды циркония, тория. Они позволяют получать изделия с высокими температурами плавления (до 2500-3000В°С), что имеет значение в реактивной технике, радиотехнической керамике. Материалы высшей огнеупорности изготовляют на основе карбидов, нитридов, боридов, силицидов, сульфидов. Некоторые из них имеют температуры плавления до 3500 - 4000В°С - группа карбидов.
Большой практический интерес имеют керметы, состоящие из металлической и керамической частей с соответствующими свойствами. Получили признание огнеупоры переменного состава. У этих материалов одна поверхность представлена чистым тугоплавким металлом- вольфрамом, другая - огнеупорным керамическим материалом- оксидом бериллия. Между поверхностями в поперечном сечении состав постепенно изменяется, что повышает стойкость материала к тепловому удару.
Для строительной керамики вполне пригодна глина, которая является распространенным в природе сырьем. В сочетании с добавочными материалами из нее получают в керамической промышленности разнообразные изделия в широком ассортименте. Их классифицируют по ряду признаков.
По конструкционному назначению выделяют: изделия стеновые, фасадные, для пола, отделочные, для перекрытий, кровельные изделия, санитарно-технические изделия, дорожные материалы и изделия, для подземных коммуникаций, огнеупорные изделия, теплоизоляционные материалы и изделия, химически стойкую керамику.
По структурному признаку все изделия разделяют на две группы:
Пористые керамические изделия впитывают более 5% по весу воды (кирпич обыкновенный, черепица, дренажные рубы).В среднем водопоглощенипористых изделий составляет 8 - 20% по весу или 15 - 35% по объему.
Плотными принимают изделия с водопоглощением меньше 5% по массе, и они практически водонепроницаемые, например плитки для пола, канализационные трубы, кислотоупорный кирпич и плитки, дорожный кирпич, санитарный фарфор. Чаще всего оно составляет 2 - 4% по весу или 4 - 8% по объему. Абсолютно плотных керамических изделий не имеется, так как испаряющаяся вода затворения, вводимая в глиняное тесто, всегда оставляет некоторое количество микро- и макропор.
3.Виды керамических материалов и изделий
Стеновые материалы и изделия.
Применяют: для возведения внутренних и наружных стен, а также для изготовления стеновых панелей.
Камни изготавливают следующих размеров:
Вид камня |
|
|
|
Обычный |
250 |
120 |
138 |
Модульный |
288 |
138 |
138 |
Сборные изделия из кирпича и керамического камня – изготавливаются в виде керамических стеновых панелей и блоков для наружных стен на заводах, которые позволяют сделать кирпич более индустриальным.
Изделия для внешних и внутренних облицовочных работ.
Изделия для облицовки фасадов:
лицевой кирпич и камень изготавливают методом пластического формования или полусухого прессования с нанесением фактурного слоя или без него, имеет две лицевые поверхности – ложковую и тычковую;
двухслойный кирпич формуется из местных красных глин, и только лицевой слой (3…5 мм) из белообжиговых глин;
глазурованный кирпич – лицевая поверхность покрыта глазурью;
ангобованный кирпич – лицевая поверхность покрыта ангобом;
коврово-мозаичные плитки – для отделки внутренних и внешних стен жилых и гражданских зданий.
Плитка для внутренней облицовки.
В соответствии с применяемым сырьем их разделяют на два вида:
майолика (легкоплавкие глины +20 % мела + глазурь);(рис.8)
(рис.8)
фаянсовые (огнестойкие глины + кварцевый песок + плавкие добавки + глазурь).(рис.9)
рис.9
Для внутренней облицовки применяют
плитки с размерами, как правило: . Толщина плитки не
должна превышать 6 мм, водопогрлощение – 16 %. К качеству плитки
предъявляются высокие требования – правильная геометрическая форма, четкие
грани и углы, термическая стойкость.
Плитка для пола
Керамические плитки для пола могут быть глазурованными и не глазурованными, с гладкой и рифленой поверхностью и должны иметь правильную форму с размером 50…150 мм, толщиной 10…13 мм. (рис.10)
(рис.10)
Их изготавливают из тугоплавких или огнестойких глин с красящими добавками или без них. Плитки должны иметь высокую прочность, водопоглощение до 5 %, повышенное сопротивление стиранию.
Теплоизоляционные
керамические материалы.
Керамические изделия применялись для теплоизоляции домов ещё во времена глубокой древности. В наше время искусственно обожжённые материалы не потеряли своей актуальности. Широко применяются такие теплоизоляционные керамические материалы, как пористый, глиняный кирпич, диатомовый кирпич, штучные изделия из обожжённой глины и керамзит.(рис.11)
рис.1
Диатомовые материалы или трепел высушивают и перемалывают в порошок тонкой консистенции. Затем подобно глине его замачивают в воде, делают замес, формируют теплоизоляционное изделие по форме, в виде кирпича, плитки или скорлупы, сегмента. Затем, так же как и печной кирпич высушивают и обжигают в печах.
Иногда для придания пористости в них добавляют выгорающие добавки во время замеса. Эти пластические вещества при обжиге выгорают и придают теплоизоляционному материалу больше пористости и увеличивают эффективность. Подразделяются эти теплоизоляционные керамические материалы на марки: пятьсот, шестьсот, семьсот килограмм на один метр кубический. И обозначает эта маркировка их объёмный вес. Эти изделия, как и кирпич, имеют низкую теплопроводность. Их можно применять для теплоизоляции плавильных печей имеющих перепады температур от триста пятидесяти до девятисот градусов.
Стеновые материалы (кирпич глиняный обыкновенный, пустотелый и легкий, камни керамические пустотелые);(рис12)
|
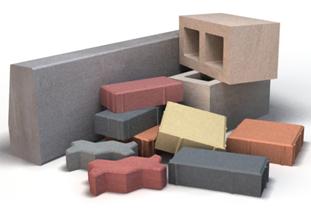
Кровельные материалы и материалы для перекрытий (черепица, керамические пустотелые изделия);(рис.14)
|
Облицовочные материалы для наружной и внутренней облицовки (кирпич и камни лицевые, плиты керамические фасадные, малогабаритные плитки)(рис.15)
|
Материалы специального назначения (дорожные, санитарно-строительные, химически стойкие, материалы для подземных коммуникаций, в частности трубы, теплоизоляционные, огнеупорные);(рис.16)
|
Заполнители для легких бетонов (керамзит, аглопорит)(рис.17)
|
По температуре плавления керамические изделия и исходные глины разделяются на легкоплавкие (с температурой плавления ниже 1350В°С), тугоплавкие (с температурой плавления 1350-1580В°С) и огнеупорные (свыше 1580В°С).
Отличительная особенность всех керамических изделий и материалов состоит в их сравнительно высокой прочности, но малой деформативности. 4. Общие свойства керамических материалов и изделий.К керамическим материалам предъявляются различные требования соответственно тем воздействиям, которые они испытывают при использовании их в строительстве. В связи с этим необходимо знать основные свойства керамического материала и пути их регулирования в процессе изготовления различных керамических изделий.
4.1 Водопоглощение керамических материалов
характеризует количественную величину их пористости и соответственно
степень спекания, которая в свою очередь влияет на многие рабочие свойства
изделий строительной керамики: морозостойкость, паро и воздухопроницаемость,
сцепление с раствором, загрязняемость и д. р. Диапазон этого показателя для
изделий строительной керамики в зависимости от их вида и назначения довольно
велик - от 1 - 30%.
Предел прочности при сжатии Rсж керамических материалов зависит от их состава и структуры и уменьшается с увеличением размера образца. Важное значение Rсж имеет для изделий стеновой керамики, которые воспринимают большие нагрузки в зданиях и сооружениях. По этому показателю стеновые изделия маркируют, принимая за марку среднюю величину по результатам испытания пяти образцов. Для изделий строительной керамики Rсж находится в пределах 7,5-70 МПа.
Предел прочности при изгибе керамических материалов Rиз зависит от тех же факторов, что и Rсж, с той лишь разницей, что здесь структура материала оказывает более резкое влияние на его сопротивляемость изгибу. Для керамических материалов Rиз находится в пределах 0,7-5 МПа.
4.2 Морозостойкость
керамических материалов
называют способность материала в насыщенном водой состоянии выдерживать многократное попеременное замораживание или оттаивание без признаков разрушения и без значительного понижения прочности. Показателем морозостойкости является количество теплосмен, которое выдерживает материал без признаков разрушения.
Обстоятельные исследования по влиянию гранулометрии пор на морозостойкость керамических материалов выявили следующие положения:
все поры в керамическом материале могут быть разделены на три категории: опасные, безопасные и резервные;
Опасные поры заполняют водой при насыщении на холоду. В них она удерживается при извлечении материала из воды и замерзает при температуре от - 15 до - 20 ºС.
Диаметр этих пор от 200 до 1 мк для глиняного кирпича пластического прессования, от 200 до 0,1 мк для глиняного кирпича полусухого прессования;
безопасные поры при насыщении на холоде водой не заполняются, либо заполнившая их вода не замерзает при указанных температурах. Это обычно мелкие поры. Заполняющая их вода становится по существу пристеночной адсорбированной влагой, имеющей свойства почти твердого тела и температуру замерзания существенно ниже (-20 ºС);
резервные поры при насыщении на холоде полностью заполняются водой, но из них при извлечении образца из насыщенного сосуда вода частично вытекает вследствие малых капиллярных сил. Это крупные поры диаметром более 200 мк.
Согласно этим исследованиям, керамический материал будет морозостойким, если в нем объем резервных пор достаточен для компенсации прироста объема замерзающей воды в опасных порах.
Морозостойкость определяет долговечность керамических материалов при их службе в условиях воздействия на них внешней среды. Поэтому требования морозостойкости регламентированы ГОСТами для стеновых, фасадных, кровельных и некоторых других изделий строительной керамики.
Керамические изделия по морозостойкости подразделяют на марки Мрз15, Мрз25, Мрз35, Мрз50. Марка морозостойкости соответствует количеству теплосмен, которое изделие должно выдерживать без каких-либо признаков видимых повреждений.
Теплопроводность керамических
материалов зависит от их объемной массы, состава, вида и размера пор и резко
возрастает с увеличением их влажности, так как теплопроводность воды выше
теплопроводности воздуха в 20 раз.
Замерзание воды в порах материала ведет к дальнейшему резкому возрастанию его
теплопроводности, поскольку теплопроводность льда
больше теплопроводности
абсолютно плотного керамического черепка
примерно, в 2 раза,
больше теплопроводности воды в 4 раза и больше теплопроводности воздуха в 80
раз.
5.Сырье для изготовления керамики
Глинами называют осадочные породы, представляющие собой тонкоземлистые минеральные массы,способные независимо от их минералогического и химического состава образовыватьс водой пластичное тесто, которое после обжига превращается в водостойкое ипрочное камневидное тело.
Состоят глины из теснойсмеси различных минералов, среди которых наиболее распространенными являютсякаолинитовые, монтмориллонитовые и гидрослюдистые. Представителями каолинитовыхминералов являются каолинит и галлуазит. В монтмориллонитовую группу входятмонтмориллонит, бейделлит и их железистые разновидности. Гидрослюды — восновном продукт разной степени гидратации слюд.
Наряду с этими минераламив глинах встречаются кварц, полевой шпат, серный колчедан, гидраты окисловжелеза и алюминия, карбонаты кальция и магния, соединения титана, ванадия. Такиепримеси влияют как на технологию керамических изделий, так и на их свойства.Например, тонко распределенный углекислый кальций и окислы железа понижаютогнеупорность глин. Если в глине имеются крупные зерна и песчинки углекислогокальция, то при обжиге из них образуются более или менее крупные включенияизвести, которая на воздухе гидратируется с увеличением объема (дутики), чтовызывает образование трещин или разрушение изделий. Соединения ванадия служатпричиной появления зеленоватых налетов (выцветов) на кирпиче, что портитвнешний вид фасадов.
Глины часто содержат также органические примеси. По отношению к действию высоких температурразличают глины трех групп: огнеупорные (огнеупорность выше 1580"С),тугоплавкие (1350 — 1580"С) и легкоплавкие (ниже 1350"С). К огнеупорнымотносятся большей частью каолинитовые глины, содержащие мало механическихпримесей. Такие глины используют для производства фарфора, фаянса и огнеупорныхизделий. Тугоплавкие глины содержат окислы железа, кварцевый песок и другие примесив значительно большем количестве, чем огнеупорные, и применяются для производства тугоплавкого, облицовочного и лицевого кирпича, плиток
для полов иканализационных труб.
Легкоплавкие глины наиболее разнообразны поминералогическому составу, содержат значительное количество примесей(кварцевого песка, окислов железа, известняка, органических веществ).Используют их в кирпичном и черепичном производствах, в производстве легкихзаполнителей и т. д.
В производствеискусственных обжиговых материалов можно применять также некоторые другиеосадочные породы: диатомиты, трепелы и их уплотненные разновидности — опоки, атакже сланцы в чистом виде и с примесью глин или порообразующих добавок.
Наиболее часто глины состоят при
преобладающем количестве минерала каолинита и
подобных ему минералов. В глинах могут быть примеси карбонатов, оксидов железа,
кварца, известняка, которые существенно влияют на свойства керамических
материалов. Например, цвет зависит от наличия в глине оксидов железа; железная
руда снижает температуру плавления.
Кроме глины к применяемым порошкообразным материалам, являющимися главными компонентами керамических изделий, относятся также некоторые другие минеральные вещества природного происхождения - кварциты, магнезиты, хромистые железняки.
5.1 Свойства глины
Глинистое сырье для керамических материалов характеризуется:
1). Гранулометрическим (зерновым) составом глины:
глинистые - до 0,001 мм;
пылеватых – от 0,001 до 0,14 мм;
песчаных – от 0,14 до 2 мм;
включения - зерна кварца величиной > 5,0 мм.
2). Пластичность глины – свойство
глиняного теста деформироваться под нагрузкой без образования трещин и разрывов
и сохранять форму после снятия этой нагрузки. Физически показателем
пластичности называют число пластичности :
,
где -
влажность, при которой глина переходит из пластичного состояния в текучее,
называемое нижней границей текучести;
- влажность, при которой глина
переходит из пластичного состояния в хрупкое, называемое границей раскатывания.
По пластичности глины разделяют:
·
высокопластичные ;
·
среднепластичные ;
·
умереннопластичные
;
·
малопластичные ;
· пластичные.
3). Усадка – называется изменение
линейных размеров и объема образца в процессе сушки (воздушная усадка
2÷12 %) и обжиговая (2÷8 %). Полная усадка
соответственно есть сумма данных усадок, и находится в пределах
4). По огнестойкости глинистое сырье разделяют на классы:
·
«О» - огнестойкие
с показателем огнестойкости
·
«Т» -
тугоплавкие,
·
«Л» -
легкоплавкие,
6.Добавки, для улучшения свойств глины: отощающие, выгорающие и пластифицирующие добавок.
Для улучшения природных свойств глины – уменьшение общей усадки, чувствительности к сушке и обжигу, улучшения формовочных свойств – широко применяют добавки. Добавки, используемые при производстве кирпича и керамических камней, по назначению можно разделить на:
Отощающие – песок, шамот, дегидратированная глина, уносы керамзитового производства и другие минеральные невыгорающие добавки;
отощающие и выгорающие полностью или частично – древесные опилки, лигнин, торф, лузга, многозольные угли, шлаки, золы ТЭЦ, отходы углеобогатительных фабрик;
выгорающие добавки в виде высококалорийного топлива – антрацит, вводимые в массу для улучшения обжига изделий;
обогащающие и пластифицирующие добавки – высокопластичные жирные и бетонитовые глины, сульфитно-спиртовая (ССБ);
упрочняющие флюсующие добавки- пиритные огарки, отходы стекла.
Отощающие добавки
В качестве отощителя следует применять кварцевый песок. Пески карбонатных пород или засоренные карбонатом не допускаются. Необходимо использовать крупнозернистые пески (от 1,5 до 0,15 мм). Мелкозернистые почти не уменьшают усадку и чувствительность изделия в сушке и в то же время снижают прочность изделия.
Шамот получают из обожженных отходов керамических изделий. Он является более эффективным отощителем, чем кварцевый песок.
|
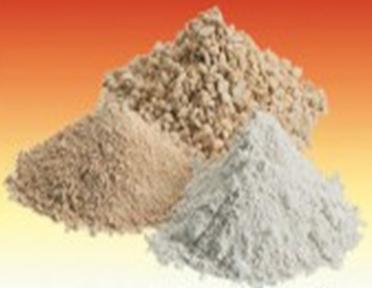
Применяют древесные опилки продольной и поперечной резки.
Предпочтения следует отдавать опилкам продольной резки.
Так как опилки длинноволокнистые, то они армируют глиняную массу и повышают ее сопротивление разрыву, а вместе с теми трещиностойкость во время сушки. Опилки улучшают формовочные свойства глиняной массы, но снижают прочность изделий, повышают водопоглащение. Применение опилок при производстве полнотелого и пустотелого кирпича снижает объемную массу кирпича и соответственно улучшает его теплозащитные свойства.
В ряде случаев добавка 5-10% опилок повышает морозостойкость кирпича и камней. При значительном количестве опилок в составе шихты ухудшается внешний вид изделия и снижается прочность. Наибольший эффект от применения опилок в качестве добавки получают, когда вводят их в сочетании с минеральными отощителями, например с шамотом, а также с углем.
Лигнин является отходом производства древесного спирта и представляет собой не только отощающую и выгорающую добавку, но и пластификатор. (рис.20)
|
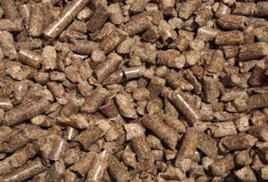
Использование лигнина в качестве добавки к пылеватым суглинкам, чувствительным к сушке, улучшает их формовочные свойства и снижает трещинообразование изделий при сушке. В качестве выгорающей добавки лигнин улучшает качество обжига. Добавляют 6-20% лигнина от объема массы. Для получения пористого кирпича количество его можно доводить 40%.
Измельченный (фрезерный) торф и отходы торфяных брикетов при отсутствии других отощителей могут служить добавкой в глину при производстве пористого облегченного кирпича.
Топочные шлаки являются эффективной отощающей добавкой. Особенно это относится к их стекловатой части.
Шлаки снижают чувствительность изделий к быстрой сушке. Значительно улучшается качество обжига, и устраняют трещины вовремя сушки при добавке шлаков высокой калорийности в сочетании с небольшим количеством опилок (до8%).
5. Золы ТЭЦ представляют собой отходы от сжигания в пылевидном состоянии каменных углей.
Образующиеся зола и шлаки направляются от котельных теплоэлектростанций гидравлической системой в золоотвалы в виде пульпы. В кирпичном производстве в качестве добавки используют золы ТЭЦ с удельной поверхностью 2000-3000 см. Теплотворная способность золы в зависимости от содержания несгоревших частиц топлив составляет от 1000 до 3200 ккал/кг
Добавка 10-15% золы ТЭЦ в смеси с опилками или шамотом делает кирпич менее чувствительным к сушке и повышает его прочность по сравнению с добавкой, например, одного дробленого многозольного угля или одних опилок. Это происходит вследствие того, что предварительное смешивание с другими добавками обеспечивает более равномерное распределение золы и
Отходы углеобогащения получают после обогащения различного угля. Они представляют собой глинистые, сланцевые породы с содержанием горючей части 10-30%, отличающиеся высокой теплотворной способностью.
Влажность углесодержащих пород 10-12% и более, крупность кусков неслипшейся породы от 6 до 100 мм, зольность в среднем 70%. Встречаются породы с большим содержанием глинозема и угля, которые используют в качестве отощающих добавок. В суглинках с небольшим содержанием глинозема их применяют как обогащающие добавки глин и прочность изделий.
Выгорающие добавки
К этой группе относится различные виды твердого топлива, в частности антрацит и коксовая мелочь.
и
Их вводят в состав шихты до 3% по объему, т.е. до60-80% от общей потребности топлив на обжиг изделий. Назначение их интенсифицировать процесс обжига, улучшать спекаемость массы и тем самым повышать прочность изделий. Выгорающие добавки целесообразно вводить в пылевидном состоянии.
Обогащающие и пластифицирующие добавки
Для обогащения малоглиноземистого сырья (с содержанием глинозема 6-8%) и увеличения его пластичности в качестве добавки применяют более пластичную и с большим содержанием глинозема глину в количестве 10-12% и более от общего состава массы. С целью лучшего смешивания сырья двух видов и уменьшения количества добавляемой высокопластичной глины ее рекомендуется вводить в виде суспензии с влажностью примерно 40%.
Пластифицирующими материалами
могут служить также вытяжки из соломы и торфа, которые вводят в глиняную массу
при ее затворении вместе с обычной водой.
Добавку можно широко использовать па многочисленных мелких
кирпично-черепичных предприятиях в сельскохозяйственных районах с
малопластичным сырьем. Для приготовления соломенной вытяжки солому предварительно
машиной превращают в сечку, загружают в емкость с водой и кипятят в течение 15
мин. Соломенной сечки берут из расчета 1,0–1,5 кг на 10 л воды. Глиняную массу
затворяют полученным отваром, разбавленным пополам с водой. Вытяжку из соломы
можно готовить и на холодной воде с добавлением в нее NaOH до получения 1%-ного
раствора.
Одним из пластифицирующих поверхностно-активных веществ, улучшающих формовочные
свойства глиняной массы, может служить сульфитно-спиртовая барда (ССБ),
являющаяся отходом производства целлюлозы.
Для улучшения декоративного вида и стойкости к внешним воздействиям поверхностный слой керамических изделий покрывают:
глазурью – легкоплавкие, прозрачные и непрозрачные стекла, окрашенные и неокрашенные. Основные компоненты глазури – кварцевый песок, каолин, полевой шпат, соли щелочных и щелочноземельных металлов, оксиды. Глазурь в виде шликера наносят на поверхность изделия и обжигают в печах до расплавления;
а. б.
Рисунок 1. а – глазурь; б - ангоб
ангобом – белая или цветная глина, нанесенная на поверхность изделия тонким слоем в виде шликера и выпаренная. Ангоб не плавится и покрытая им поверхность выглядит матовой.
7.Получение керамики. Порошки для изготовления керамики.
Требования к порошкам для получения керамики в зависимости от ее целевых свойств могут быть различными, с другой стороны к наиболее общим из них относятся следующие: заданный химический, фазовый и гранулометрический состав, их однородность, активность и пр.
Методы получения порошков можно разделить принципиально на две большие группы: основанные на диспергировании (измельчении) исходных материалов и наоборот на их конденсации, т.е. выделении твердых веществ из жидкой или газообразной фазы.
Методы первой группы подразделяются в зависимости от принципов, положенных в основу процессов диспергирования: истирание, удар, давление, взрыв, ультразвуковое воздействие, электромагнитный импульс, электроискровое или дуговое диспергирование, электрохимическая или химическая коррозия, лазерное воздействие, разрушение материала за счет последовательных теплосмен и пр.
Ко второй группе относятся, например, разложение металлоорганических соединений (МОС), различные варианты осаждения из растворов, упаривание солевых растворов, осаждение за счет реакций в газовой фазе, конденсация паров, криохимический метод, распылительная сушка и т.д. Особенностью получения порошков таких материалов, как сложные оксиды, является то, что в его ходе часто протекают химические реакции разложения исходных веществ (солей, органических соединений, гидроксидов и т.п. термически непрочных форм), а далее осуществляется твердофазный синтез фаз заданного состава. Методы получения компактных сложнооксидных материалов можно подразделить на собственно керамические и методы с использованием растворных (в частности, солевых) технологий ( Таблица 1).
|
Анализ и подготовка исходного сырья
Важное место при получении керамики занимает анализ и подготовка исходного сырья, в котором, в частности, необходимо определение содержания основного вещества, индифферентных и нежелательных примесей, гранулометрического, фазового состава. Последний часто находится во взаимосвязи с активностью исходных реагентов. Так при получении различных ферритов по керамической технологии наиболее активной формой используемого оксида железа является g-Fe2O3, ее наличие значительно ускоряет протекание синтеза. Определение соотношения количества этой формы и других модификаций проводят методом рентгенофазового анализа или при помощи термического анализа на дериватографе, используя то, что при температуре около 560оС происходит переход g-Fe2O3--> a-Fe2O3, сопровождающийся экзотермическим эффектом, интенсивность которого связана с количеством активной фазы.
Дозирование
Дозирование проводят с максимально возможной точностью, как правило применяя весовые формы исходных веществ. Часто требуется предварительное прокаливание реагентов для удаления адсорбированной из окружающей среды влаги, углекислого газа и др., либо необходим учет коэффициента потерь при прокаливании.
Смешивание и помол
Смешивание реагентов часто совмещается с их дополнительным измельчением (помолом). Агрегатами, используемыми с этой целью, являются наиболее часто применяемые шаровые или роликовые барабанные и вибрационные мельницы. В чистом виде (без измельчения) операция смешивания осуществляется во вращающихся смесителях разных типов: биконических, V-образных, смесителях “пьяная бочка”
Критерием полноты процесса смешивания является поверхность раздела смешиваемых фаз S. Протекание смешивания описывается уравнением:
dS/dt = -K(Smax - S).
После разделения переменных и интегрирования получим:
-1/kln(Smax-S) = t или S = Smax - e-kt .
Поверхность раздела реагентов, увеличиваясь во времени, асимптотически приближается к максимально возможной, исходя из геометрии частиц.
|
Удельную поверхность оценивают, например, методом измерения газопроницаемости (по падению скорости потока газа или давления при прохождении его через стандартный порошковый образец), для чего необходимо первоначально осуществить калибровку по порошкам с известной поверхностью. Один из надежных способов - низкотемпературная сорбция газов (азота и др.) с тепловой десорбцией, определение количества сорбированных газов проводят волюметрическим, гравиметрическим и др. методами.
Эффективным приемом улучшения качества измельчения материалов выступает использование жидких сред помола, а также добавок поверхностно активных веществ (ПАВ). Это позволяет избежать явления самозалечивания трещин в частицах за счет адсорбции на вновь возникающих поверхностях молекул жидкостей и ПАВ и их расклинивающего действия. Наличие адсорбирующихся веществ вносит дополнительный вклад с точки зрения энергетики разрушающих сил. В качестве среды помола берут обычно воду, в тех случаях, когда её присутствие нежелательно из-за гидролитического действия на порошки (например, YBa2Cu3O7-d ), используют спирты, кетоны и пр., которые удобны тем, что затем легко удаляются при сушке шихты.
Рассмотрим особенности использования распространенных агрегатов измельчения.
Шаровая барабанная мельница
Шаровая барабанная мельница имеет следующие достоинства:
простота конструкции и использования;
хорошее смешивание материалов (коэффициент неоднородности порядка 3-5%);
Недостатки:
длительность процессов;
невысокий объемный коэффициент загрузки (40-45%);
значительный намол аппаратурного металла.
Измельченные материалы имеют довольно широкую кривую распределения частиц по размерам.
Существует эмпирическая формула расчета диаметра пригодных шаров d: d=iЦ3D, здесь D - диаметр мельницы; i - коэффициент, равный 2,5. Скорость вращения выбирается в пределах 0,78 0,8nкр.(обычно 60-100 об/мин): nкр.=42,3/ЦD. При значениях 0,4-0,6 происходит скольжение и перекатывание шаров, основная сила, воздействующая на частицы - трение. При 0,78-0,8 шары захватываются стенкой, а затем падают, к силам трения добавляется ударное действие на материал. Значения nкр. более 0,8 приводят к прилипанию массы шаров и шихты к стенке.
Вибрационные шаровые мельницы.
Достоинства:
более высокий коэффициент заполнения объёма (шары до 0,75 объёма, материал - около 0,1-0,2, итого: Кзап.=80-85%);
меньшее время обработки материалов (обычно 0,5-2 часа).
Недостатки:
намол материала мельницы и шаров;
большая неоднородность при смешивании (Vнеодн. » 15%).
Данный тип мельниц целесообразно применять для измельчения.Чаще берут шары 2-3 различных диаметров для лучшего заполнения и увеличения числа контактов между ними.
Сушка. Брикетирование или гранулирование.
После помола или смешивания в мокрой среде осуществляют сушку выгруженного из мельниц материала в установках распылительной сушки, виброкипящего слоя и пр., а чаще в металлических (стальных) кюветах, используя специальные сушильные шкафы. На данном технологическом этапе важно избежать седиментационного разделения компонентов особенно после смешивания исходных материалов.
8. Общая технологическая схема изготовления керамических изделий
Несмотря на широкий ассортимент керамических изделий, основные этапы изготовления этих изделий одинаковые:
· добыча сырьевых компонентов в карьере;
· подготовка сырьевой массы (дробление, помол, добавки, увлажнение);
· формование изделий (сырец);
· сушка и обжиг;
· складирование.
Переработку сырьевой массы и формовку изделий выполняют:
Пластичный способ формовки.
Используя пластический способ формовки изделий, глину измельчают на вальцах грубого и тонкого помола, а также подвергают переработке в бегунах. После дробления глину подают в глиносмеситель, где она перемешивается с добавками до однородной пластической массы и увлажнения до влажности 20÷20 %. Такой способ предусматривает формовку изделий на ленточных прессах. Глиняный брус, который выходит из-под пресса, разрезают автоматическим резальным аппаратом на изделия заданного размера.
|
Пластичным формованием изготавливают обычный и эффективный кирпич, камни, керамические трубы.(рис.1)
Полусухой способ
формования.
При полусухом способе формования изготовления глину сначала дробят и сушат до влажности 6÷8 %, затем дополнительно повторно дробят в дезинтеграторах, просеивают, увлажняют полученный порошок паром до влажности 8÷12 % и тщательно перемешивают в глиносмесителе. Подготовленную массу прессуют на гидравлических прессах при давлении 15÷40 МПа. (рис.21)
|
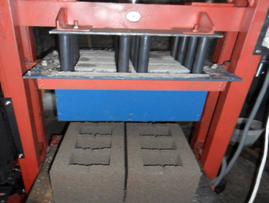
Полусухой способ экономичнее пластического, поскольку не требуется сушки изделий. Но кирпич полусухого прессования имеет меньшую морозостойкость.
Мокрый (шликерный) способ формования.
Суть способа состоит в том, что исходные материалы дробят совместно с водой в шаровой мельнице при влажности 45÷60 % до получения однородной массы – шликера.
|
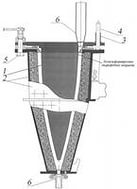
Изделия получают методом литья или полусухим прессованием (облицовочные плитки, плитки для пола).(рис 22)
Сушка и обжиг керамических материалов.
Обязательной промежуточной
операцией технологического процесса изготовления керамических изделий является
сушка, которую производят в туннельных сушках беспрерывного действия до
влажности для предотвращения
неравномерной усадки и растрескивания при обжиге.
Сырец на вагонетках движется по туннелю навстречу потока горячего воздуха или дымовых газов (16÷36 часов). Обжиг керамических изделий осуществляют в туннельных и кольцевых печах с автоматическим управлением. Максимальная температура обжига кирпича и других стеновых керамических изделий 950÷10000С, которая необходима для спекания керамической массы. Туннельная печь – длинный канал, в котором вагонетки с изделиями проходят три зоны: подогрева, обжига, охлаждения.(рис.2)
Рисунок 2 .
а – туннельная печь Гипрострома (Киев): а). – зона подогрева; б – зона взвара (1 – кладка печи; 2 – воздухопровод; 3 – газопровод); в – схема тепловых зон; б – схема работы (а); и разрез (б) кольцевой печи: 1 – дымовые очелки; 2 – дымовой конус; 3 - дымовой канал; 4 – ходок; 5 – рассыпной строй; 6 – клапан рассыпного строя; 7 – штанга; 8 – топливные трубы
Заключение
В заключение сказанного можно подвести итоги:
· керамическими называют материалы и изделия, получаемые из порошкообразных веществ различными способами и подвергаемые в технологический период обязательной термической обработке при высоких температурах для упрочнения и получения камневидного состояния. Такая обработка носит название обжига;
· кроме глины к применяемым порошкообразным материалам, являющимися главными компонентами керамических изделий, относятся также некоторые другие минеральные вещества природного происхождения - кварциты, магнезиты, хромистые железняки;
· по структурному признаку все изделия разделяют на две группы: пористые и плотные;
· сырьевые материалы, используемые для изготовления керамических изделий, можно подразделить на пластичные глинистые (каолины и глины) и отощающие (шамот, кварц, шлаки, выгорающие добавки). Для понижения температуры спекания в глину иногда добавляют плавни.
Облицовка керамикой - один из самых экономически эффективных видов отделки фасадов и интерьеров зданий. Хотя первоначальная стоимость такой облицовки выше многих других видов отделки, но с учетом очень высокой долговечности керамики, т.е. в пересчете на один год эксплуатации, керамическая облицовка оказывается выгоднее большинства видов отделки. К несомненным достоинствам такой облицовки необходимо отнести архитектурную выразительность. Облицовка керамикой не только придает декоративность, но и защищает конструкцию от внешних воздействий.
Список литературы.
1. Ругалев Р.Т., Ивлев С.Ю.
Технология производства керамического кирпича. – Кемерово.: «Рост»,
2000г.
2. Буревич С.Б.
Строительные материалы. – Л.: «Омега», 1987 г.
3. Рабинович В.А., и др.
Краткий химический справочник. – Л.: «Химия»,1979 г.
4. Мальцев И.М.
Материаловедение. – Ниж. Новгород.: «НГТУ», 1996 г.
5. Карабасов Ю.С.
Новые материалы. – М.: «Масис»,2003 г.
6. Сажин В.Б.
Основы материаловедения. – М.: «Теис»,2007 г.
7. Новые материалы /
под науч. ред. Ю.С. Карабасова, - М.: Мисис, 2002
8.Основы материаловедения / Сажин В.Б. - М.: Теис,
2005
9. 9.https://ru.wikipedia.org
10. http://www.materialsworld.ru